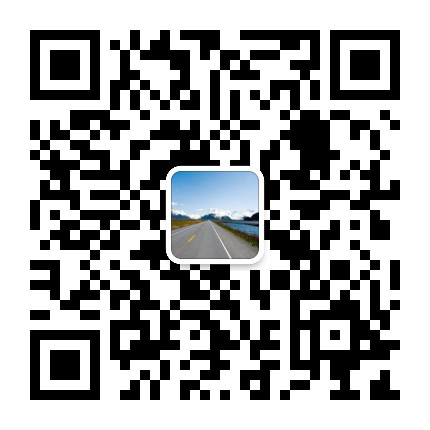
和田蔡司工业ct在无需破坏实际工件情况下生成实际部件的3D模型的能力使得计算机X射线分层技术在工件检测方面变得极为重要。工件的3D图形可显示出包括内外几何形状在内的整体部件情况。
此外,X射线分层系统还可以对复杂工件进行高精尺寸测量。因此无需再把部件浇注到合成树脂里,再逐步破坏树脂,以进行2D分层测量。这种计算机X射线分层技术的另一个优点是:测量结果容易解读。与传统的测量记录相比,制造厂商有了彩色图形更能快捷而明了地识别出,部件在哪些地方与额定状态发生了偏差。
所有材质的产品均可借助于X射线分层技术进行测量。根据材料不同的可透视性能,计算机X射线分层系统可以对部件进行1mm~0.5m长度的透视。特别容易透视的材料为塑料和硅。这种测量方法特别适用于复合材料部件,这是因为X射线可以使材料内部的纤维变得可视化。
测量过程所需时间不同,这要视对分辨率的具体要求而定。在5min测量之后,仪器即可提供第一批数据结果。但是,测量时间越长,结果则越准确。例如,在制药行业则需要有各个具体细节。重要的一点便是,测量仪器可以识别出几微米的偏差。这种情况下,测量过程往往需要1h或更长。这时系统可以识别出产品内部的所有细节。
喷注件和压铸件因材料和工艺参数(如收缩等)的不同,通常会与铸型底片不很对应。因此,模具制造往往需要一个甚至多达十个步骤的重复性流程。X射线分层技术可以降低这种循环时间,极大缩短开发时间:Carl Zeiss公司的Calypso测量软件对此可以提供“刀具校准”功能。
由此,制造厂商不仅可以测得实际外形偏差,同时也可以“镜像”反映实际表面。由此可以预先设定铸模的收缩尺寸并把测量值纳入到刀具校准程序中去。所测得的数据可以直接用作刀具二次加工的给定值。由于刀具校准工作量明显下降,因此部件可以更快上市。用户调查发现这方面的节约潜力高达50%~70%。
在塑料齿轮制造方面,X射线分层技术也是一种强有力的工具。总体上说,在测量塑料齿轮时,也必须对与钢齿轮一样的那些参数进行测量,主要的区别只在于塑料齿轮的各个齿都必须接受检测。Carl Zeiss公司的Gear Pro软件有助于对齿缘面进行描述。
这项工作是必要的,以便可以在CAD数据基础上对齿合状况进行测量。所使用的运算流程是经过认证的。